
Axion EMS (eco modula system)
eco modula GmbH is the largest manufacturer of complete solutions in steel frame construction in Central Europe using the production and design system from FrameCad. With the help of the latest computer technology and excellent production facilities, eco modula GmbH can precisely and effectively produce complete steel frame constructions from cold-bent, galvanized steel. The strategic goal of eco modula GmbH is the dissemination of professional and practical solutions for the introduction of light building structures based on a steel frame.
The level of system progress, the constant research into product development, the certificates and the procedures introduced for operational production control give eco modula GmbH a significant lead over competition from other European countries. eco modula GmbH has its own design office, where design projects (including execution projects) of objects are processed using special programming that is firmly integrated with the factory's production line. This allows projects to be implemented that are tailored to the individual needs of investors or users.
Light steel structures produced by eco modula GmbH offer many unique advantages for investors and users, for example: freedom of design and a high degree of prefabrication, fast assembly speed on site, durability and precision of execution, corrosion resistance and resistance to environmental influences, fire resistance, no need to employ qualified personnel and rent heavy equipment, lower transportation costs. The buildings, the basis of which is the steel frame supplied by eco modula GmbH, are lighter, more resistant to vibrations and do not need any seasonal technological breaks. They can be set up quickly and have better energetic parameters compared to traditional technologies. The construction work can be carried out almost all year round. The wide range of applications of light steel structures starts with residential houses and ends with commercial and industrial buildings.
The lightweight steel frames supplied by eco modula GmbH are also extremely environmentally friendly. On the one hand, their production requires less energy, on the other hand they are one hundred percent recyclable.

DESCRIPTION OF THE LIGHT CONSTRUCTION SYSTEM
A modern and lightweight construction system is based on three integrated pillars: design, production of individual parts and their manufacture of prefabricated construction elements such as wall panels, ceilings, beams, beams or columns. Delivered to the construction site, these elements are used to erect buildings or they form an interior finishing system. The production of precast construction parts is firmly integrated with production line programming.
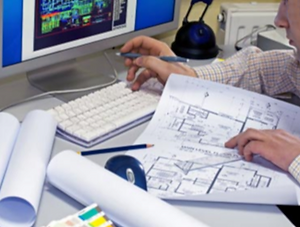


Gestaltung
Our own design office employs experienced engineers and highly qualified project engineers. The construction design runs automatically with the help of integrated programming in accordance with all standards, further referred to as Eurocode-3 (EN 1993 design of steel structures). The project engineers carry out a calculation of the statics provided with detailed rules and building standards, which was completed from construction elements.
production
Construction elements are made from cold strip profiles that have different sizes from galvanized steel strip with different thicknesses.
Every processing (cutting, making holes, punching, rolling, turning, etc.) is automatically completed in the steel profile production process.
The machine efficiency is just as high as the precision of the execution of individual profiles. Each profile has a unique automatically printed number that corresponds to the assembly plan.
Precast production
The production of prefabricated construction elements consists of the connection of finished profiles with the help of certified screws. This is actually the only job that our employees - fitters of construction elements - carry out. Your task is to connect profiles into finished construction parts. This work is supported by the precision of the profiles made together with their automatic processing.
ELEMENTS OF THE CONSTRUCTION SYSTEM
All elements are made with galvanized steel profiles type C (less often type U, which also belong to this system).
The section of a typical profile C and the geometric parameters are shown in Table 1. Changes to the sheet thickness are possible, but the size of the profiles cannot be changed

The modern and light construction system consists in the production of finished construction parts for the erection of the building. Each element has been described below so that the idea of this system can be better understood.
Wall panel system
The wall panel is the basis of the whole system. The building plan or development plan of individual floors is assembled with these finished elements. The walls are placed directly on the steel-insulated foundation plate and then connected to one another with the help of screws and set screws. Basically, this assembly is not much different from conventional walls. Thanks to its low weight, the panel can be easily aligned so that it is vertical and can be brought into plumb. The wall panels are designed as supporting and partition walls.
Below is the table that shows the standard parameters of the wall panels.
The variety of applied profiles, their thicknesses and mechanical parameters of steel strips allow a fast and precise execution of very complex construction systems, which are able to transfer the required loads. With the wall panels, the holes for the IT, electrical and heating installations are projected and automatically designed. They are even installed in the sloping joints to ensure that the electrical line is straight.
Lattice girder system.
The lattice girder is mostly constructed differently from the wall panels and ceiling beams shown above, although the profiles used for production are the same.
Ceiling panel system.
The ceiling panel is made with profile C, which is constructed in the form of a ceiling beam so that it can be "closed" with profile U at the end. With regard to the dimensions and sheet thickness, the ceiling panel is delivered to the construction site in individual profiles. Then it is attached to the supporting walls that were built earlier or to the buildings on individual floors with the help of screws and set screws. Basically, this installation does not differ much from conventional ceiling beams. The better the supporting wall panel is aligned, the easier it is to align this ceiling panel.
Below is the table that shows the standard parameters of the ceiling panels.
The type of connection between profile C and profile U to ceiling panels is facilitated by the corresponding mounting brackets, which are automatically cut out of profile U during the production process.
During the production process of profile C, holes with a diameter of 165 mm are cut out. These holes have flanges turned upside down in such a way that they significantly increase the section modulus with such a large hole. It is assumed that the standard spacing from support pillars of the ceiling panel is 6.5 meters. However, there is the option of making the ceiling beams in the form of an I-profile (U-profile connected to the "back"), which significantly increases the load-bearing capacity. In the event that the load-bearing capacity of the system made from the C254 and U260 profiles is exceeded, we will produce trusses.
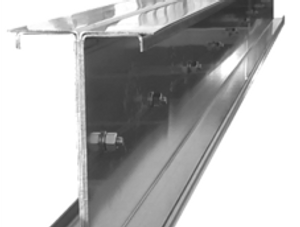
Truss system.
The truss is constructed in a similar way to a wall panel, i.e. from automatically processed type C profiles.
After the individual profiles have been installed, you get beams with a length and height that is determined by the required load-bearing capacity.
The details of the connections of individual steel profiles to a finished construction element, which can be seen in the pictures, are cutouts of the profile edges in which the screw heads are hidden and the punching of the profile ends is made automatically in the production process. After the production of the prefabricated parts, a cuboid element with uniform surfaces is created, from which no details protrude that could make the installation of the cladding (e.g. plasterboard) difficult.
The trusses are produced with both the C 89 and C150 profiles, i.e. the width of the beam is 89 or 150mm accordingly.
The maximum distance between the truss supports, which are made from certain profiles depending on the load, beam height and type, is calculated individually.


POSSIBLE USES
All the elements shown above form a construction system that is widely used in industrial, commercial and residential construction. The fast pace of the design process, the production of precast elements and the assembly contribute to reducing costs and shortening the investment period, which consequently means that the building can be released for use very quickly.


Industrial construction
The system of internal development of halls
(Room in room system).
The constructions of this kind are ideally suited for building within existing halls. In this simple way you can design additional office, social and storage rooms as well as technological rooms. The fact that the steel frame is considerably lighter compared to traditional technologies results in a huge reduction in the cost of the internal structures. The foundation for such a development is significantly easier or is not required, provided the floor has sufficient bearing capacity. The “wet” work area and the use of heavy equipment are limited. The construction is not so disruptive for the users and can be carried out without interrupting the daily activities within the existing hall. The special system of installation openings (ventilation, heating, water and electricity) in the wall panels and the ceilings is made in the prefabrication phase, which simplifies the work of the installers on site.
Server rooms.
The special case of internal development is the server room. The requirements for the ceiling load-bearing capacity or for fire resistance are usually higher.
Steel halls.
The system is also very suitable for smaller warehouses that have a span of up to 18 meters (or up to a multiple of this size). Depending on the purpose, they can be isolated accordingly and made accessible with the necessary installations or systems from the external carpentry trade, included
The steel framework system is open, which means that it can be covered with various manufacturing materials: from the sandwich panel to the traditional plaster system on Styrofoam or on mineral wool, to wood veneers and steel cassettes. The roof can be covered with cardboard, EPDM foil, sheet metal, as well as with sandwich panels, ceramic roof tiles or cement roof tiles.
Substructure for bathroom cells ..
.
Commercial construction
Construction of commercial buildings.
The system of light steel structures is also used in the construction of smaller commercial pavilions with a span of up to 18 meters (or many times this size). They are also very suitable for medium-sized office and hotel buildings up to three floors.
The buildings intended for commercial activity are erected quickly, as both the design process and the prefabrication process of the steel elements of the structure are integrated in the same factory. The system of wall panels allows us to design a building that can be erected as you wish. It allows you to design the sales area or office space variably for the respective tenant.
System of internal development of commercial buildings.
The construction system shown is also used for internal development of commercial buildings, such as supermarkets, discounters or shopping malls. In a short time, which is inaccessible for other technologies, one can design commercial, social or office spaces that are located in large-scale sales facilities that are even several thousand square meters.
System of internal development of office space.
The fast and precise design of office and social rooms on the large areas of today's office buildings is an area of application for lightweight steel scaffolding systems. Such scaffolding can be covered with practically any building material, starting with the popular plasterboard. The inner structure can be filled with mineral wool in order to achieve better acoustic properties of the partition. The assembly of the interior joinery is not problematic.



housing
Single-family houses and townhouses.
The light steel frames are suitable for the construction of both single-family and multi-family houses. The steel framework is delivered directly to the construction site as a prefabricated component of wall panels, ceiling beams and the complete roof structure. The assembly - due to the rather low weight - is quick and easy. In most cases, the assembly does not require any heavy crane equipment.
Eco Modula has its own design office, where the design projects (including execution projects) of the buildings are processed using special programming that is firmly integrated with the factory's production line.
This eliminates errors as early as the project stage. In addition, thanks to the extensive experience and knowledge of the project engineer, there is the possibility of adapting each project to the individual requirements and needs of the investor or user. The processed systems of the fire partition walls are indispensable for row and twin buildings.
Multi-storey apartment buildings
The multi-storey building means a major challenge for the light steel frame. Even so, three-story buildings can be erected fairly easily. It is possible to erect higher buildings, but in certain climatic conditions (it is snow and wind loads) you have to use additional frames made of hot-rolled steel or reinforced concrete.

FIRE PROTECTION OF THE CONSTRUCTION ELEMENTS
In the ordinance of the Minister of Infrastructure on technical conditions of April 12, 2002, to which the buildings and their location should comply, in Section IV, Chapter I, which defines in detail the terms from the field of fire protection of buildings and determines the fire protection rules, we read (the current version of the regulation can be seen on the website www.sejm.gov.pl) among others:
The building and the equipment connected to the building should be projected and constructed in such a way that in the event of a fire they will ensure:
1) the load-bearing capacity of the structure for the period following the regulation
2) limiting the spread of fire and smoke in the building
3) the restriction of the spread of the fire to nearby buildings
4) the possibility of evacuating the population, taking into account the safety of the rescue teams.
In view of the use and management of use, the buildings and the parts of the building that form separate fire compartments are divided into:
1) Residential areas, communal residential complexes and communal facilities that are characterized by the category of endangerment to humans, further referred to as ZL,
2) Production and storage buildings, further referred to as PM, 3) Rearing houses, further referred to as IN.
Buildings and parts of buildings that form separate fire compartments and are referred to as ZL belong to one or more than one of the following categories of risk to people:
1) Zl I - contain the rooms which are intended for the simultaneous stay of more than 50 people, but which do not belong to permanent users. Above all, these rooms are not intended for use by people who have limited mobility.
2) ZL II - rooms that are primarily intended for use by people with limited mobility, such as hospitals, kindergartens, crèches and retirement homes.
3) ZL III - community facilities that are not assigned to ZL I and ZL II
4) ZL IV - apartment building
5) ZL V - communal residential complexes that are not assigned to ZL I and ZL II.
Furthermore, five fire resistance classes of buildings or their building parts are determined, which are named in the order from highest to lowest and are designated with the letters: "A", "B", "C", "D" and "E". The required fire resistance class for the building belonging to one of the categories ZL is determined by the table below:

The reduction of the required fire resistance class in the buildings mentioned below is allowed to the level indicated in the table.

The required fire resistance class for the PM and IN ** building is shown in the below
Table determines:

The elements of the building that correspond to its fire resistance class should (with certain reservations) meet the requirements specified below:

Designations in the table:
R - fire resistance (in minutes) determined in accordance with the standard relating to the rules of class determination of the fire resistance of building elements
E - fire tightness (in minutes) as determined above,
I - fire insulation (in minutes) as determined above,
(-) - you don't make any demands
It is generally accepted that steel loses its mechanical properties by leaps and bounds at high temperatures, causing a sudden loss of load-bearing capacity in the structure for which it was designed. In the case of structures made of hot-rolled steel, multilayer refractory paint systems are mostly used, which swell under the influence of temperature, forming a refractory coating. The minimum thickness of the refractory protection (lower layer + layer threshold + covering layer) is determined, among other things, depending on the solidity display U / A of the concrete steel elements of the construction. Unfortunately, in the case of light steel structures, this solidity indicator is too low to use this type of fuse. In order to meet the requirements of today's construction industry, the system of lightweight steel structures should have solutions that serve to protect against fire. Frame Factory has engineered fire protection systems to be available, easy to assemble, and effectively economical.
The investigations and the classifications of these solutions were carried out in the Institute for Structural Engineering, in the Center for Ship Technology AG, in the team for research laboratories GRYFITLAB and in the FIRES laboratory in Slovakia.
Gestaltung
Eigenes Konstruktionsbüro beschäftigt erfahrene Ingenieure und hochqualifizierte Projektanten. Die Konstruktionsgestaltung verläuft automatisch mit Hilfe integrierter Progammierung gemäß aller Normen, weiter als Eurocode-3 (EN 1993 Gestaltung von Stahlkonstruktionen) bezeichnet. Die Projektanten führen eine mit detalierten Regeln und Baunormen vorgesehene Berechnung der Statik aus, die aus Konstruktionselementen fertig gestellt wurde.
Produktion
Konstruktionselemente werden aus Kaltbandprofilen hergestellt, die verschiedene Größen aus verzinktem Stahlband mit unterschiedlichen Stärken haben.
Jede Bearbeitung (Zuschneiden, Löcheranfertigung, Stanzen, Walzen, Drehen, usw.) wird automatisch im Produktionsprozess von Stahlprofilen fertig gestellt.
Die Maschineneffizienz ist genau so hoch wie die Präzision der Ausführung einzelner Profile. Jedes Profil hat eine einzigartige automatisch gedruckte Nummer, die mit dem Montageplan übereinstimmt.
Fertigteilherstellung
Die Fertigteilherstellung fertiger Konstruktionselemente besteht in der Verbindung angefertigter Profile mit Hilfe attestierter Schrauben. Das ist eigentlich die einzige Tätigkeit, die unsere Mitarbeiter – Monteure von Konstruktionselementen ausführen. Ihre Aufgabe ist, Profile in fertige Konstruktionsteile zu verbinden. Diese Arbeit wird durch die Präzision der angefertigten Profile zusammen mit ihrer automatischen Bearbeitung unterstützt.

TECHNOLOGY
cold-formed steel (CFS) - SYSTEM:
The light steel frame (cold-formed steel - kS) is an alternative technology to conventional construction. We offer customization of every project in kS technology. The main advantage of the system is that it can be implemented very quickly regardless of the season. The constructions consist of steel profiles that are protected from corrosion by a zinc layer. The profiles are then riveted together to form panels of various sizes
joined to transport them to the construction site. Wall, ceiling, roof and roof truss panels are joined on the construction site with self-tapping screws. The profiles have factory-cut service holes for internal installations. The production and assembly of the skeleton for a medium-sized residential building is possible in a week. The kS system does not generate any waste on the construction site. Steel is completely convertible. KS technology is environmentally friendly. The system enables very good thermal insulation with low wall thickness.
2019
founding year
Projects completed
47
Contractor appointed
Awards won
APPLICATION AREAS
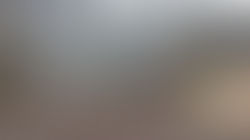

CONTACT
Second office
Mariendorfer Damm 147
12107 Berlin
Tel: +49 178 730 4995
Tel Mobil +49 178 730 4995
Fax: +49 30 2388 3967
Headquarters of Hungary
Requests
For inquiries, questions or recommendations, please contact: +49 (0) 30 2388 3969 or fill out the following form
Production facility
Münstersche Str. 18,
14772 Brandenburg an der Havel
Tel: +49 30 2388 3969
Tel Mobil +49 178 730 4995
Fax: +49 30 2388 3967
Headquarters of Poland
Czeremchowa 14,
70-763 Stettin, Polen
Tel Mobil +49 178 730 4995
Fax: +49 30 2388 3967

employment
To apply for a position at Sphere Constructions, please send a cover letter along with your C.V. to: