Advantages of the kS system at a glance:
cold formed steel (CFS)
Good buildings come from good people, and good design solves all problems.
Stephen Gardiner,
Architekt, Lehrer, Schriftsteller

Introduction.
As a construction professional, you know that building is a balancing act, especially when it comes to translating architectural intentions into safe, compliant and constructible buildings and when time and mistakes cost money. In view of the increasing global demand for high-quality, quick-to-build buildings, traditional construction methods are becoming obsolete, as new, faster, technology-enabled building processes are the be-all and end-all. So it is obvious that modern construction methods such as Cold Formed Steel (CFS) meet the requirements of the industry. Why? Because, through the use of software, design-driven methods shift design skills up and create more accurate designs that require fewer skilled workers at the end of the design process. And with the right design and engineering, such as FRAMECAD's CFS software, computer-aided automation of CFS design and engineering is made possible. This reduces the dependency on highly qualified, expensive engineering resources, accelerates the specification and compliance process and optimizes the building design. The results? More precise, cheaper, faster to erect quality buildings. And the ability to create highly scalable construction companies that achieve a much faster ROI than traditional methods.
This guide explains the concept of design-based design and specifically explains how the CFS design process differs from traditional methods. Since FRAMECAD is a leader in the development and construction of CFS with innovative software, we explain the specific advantages of the FRAMECAD design and construction process and the advantages of using FRAMECAD software over other industry alternatives.

What is design-oriented building?
Design-oriented design methods use software and manufacturing technology to produce components with a high degree of accuracy. This approach reduces engineering efforts and the need for skilled design workers, which in turn significantly reduces on-site errors and material waste. These methods typically have mature, integrated software platforms that automate the design, engineering, manufacturing, and engineering processes of a project. That is, most of the project expertise lies in the design and detailing phase of the work.
How does design-oriented building differ from conventional methods?
With traditional construction methods, decisions are made on site, with the builder's skills playing an important role in the work. Using a design-led construction process, skill moves upstream; Decision-making responsibilities are transferred to the designers and are no longer the domain of the on-site staff.
Hence the size and competence of the local workforce is essential for design-oriented methods
required, much less than with conventional construction methods.
How is that possible?
The fundamental difference between traditional methods and design-driven construction methods is the integration of sophisticated software that streamlines and connects every step of the design and creation process.
Cold Formed Steel or CFS is also known as Light Gauge Steel or LGS. CFS buildings are designed with special computer-aided design and development software and are manufactured by rolling or pressing steel into semi-finished or finished products at ambient temperature.
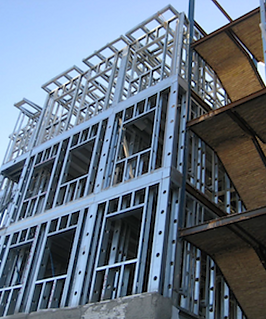
A comparison between traditional design methods and design-guided CFS design.
Traditional methods
1. Architectural packages, e.g. CAD designs the building as a concept with no practical and integrated technical data on how the building must be put together to make it safe, compliant and livable.
2. The project owner then works with an engineer who translates the architectural drawings into a designed plan and detailed construction plan, which can then be submitted for approval by the building authorities. [Time and cost increase]
3. If problems are found, the project owner must revise and resubmit the drafts and technical plans. [Time and cost increase]
4. The constructed design is then reviewed by the local authority, who confirms that the design meets the requirements of the building codes and that all calculations for the construction with the selected materials are reasonable in the given environment.
5. Depending on the method, other third-party software may create a material take-off plate but not shop drawings, making the manufacturing and assembly more complex and lengthy. [Time and cost increase]
6. Most traditional applications do not generate a complete bill of materials. This is done independently of one another with separate software. [Time and cost increase]
7. Traditional methods such as wood, concrete and brick construction have limited or no manufacturing components off-site, so manufacturing and assembling the components is left to the skilled workers on site.
8. Traditional methods require skilled labor on site (e.g., carpenters, concrete layers, brick layers), heavy lifting equipment, storage and expensive tools. [Time and cost increase]
Design oriented methods like CFS
1. Drafts can either be created in CAD and imported or designed in the engineering software itself. [Time and cost reduction]
2. With construction software with extended construction functions such as FRAMECAD Structure
Automated construction calculations and reports on components can be created. Code compliance calculations are performed in real time, enabling immediate design corrections without the need for input from the engineer.
3. Executed plans that are unlikely to be rejected. When changes are requested, they can be made quickly and in real time without costly delays. [Time and costs decrease].
4. Design that is unlikely to be rejected by the local authority. [Time and cost reduction]
5. The software creates a detailed set of shop floor and assembly drawings that allow easy manufacture and assembly, avoiding errors and rework. [Time and cost reduction]
6. The software generates a full BOM report as well as a detailed design file that organizes the production of the components so that the build can be completed as efficiently as possible. [Time and cost reduction]
7. Depending on the design method, the design software is integrated into production in order to produce components (e.g. frames and trusses) for the parts list and to optimize material consumption with practically no waste.
8. Depending on the method and components used, pre-assembled components can be transported to the construction site (in some cases on-site manufacturing can be done) and assembly can be done quickly and accurately with local, less skilled labor and basic tools. [Time and cost reduction]
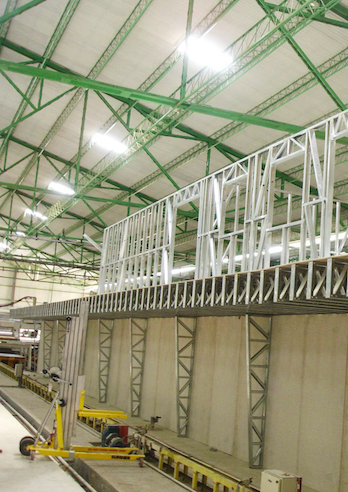


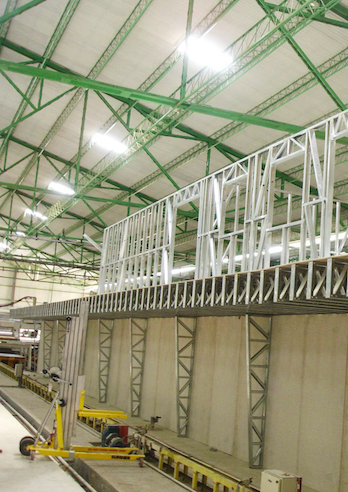